A Deep Dive into Fusion 360 CAD: Features and Uses
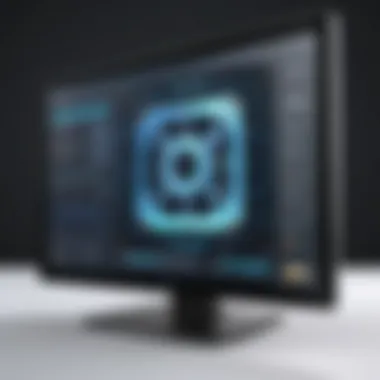
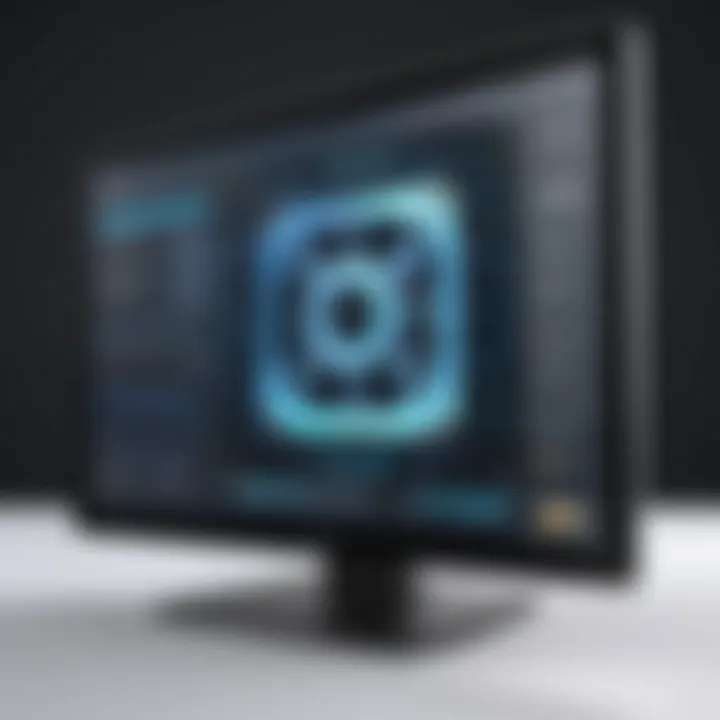
Intro
Fusion 360 CAD has become an essential tool in the realms of computer-aided design and manufacturing. It serves a multitude of purposes, appealing to both professionals and students. This article aims to dissect the various features, applications, and implementation strategies of Fusion 360, providing insights into how it influences design workflows.
Understanding software like Fusion 360 is crucial for anyone in the IT-related fields, as it offers a range of functionalities that streamline the design process. With its unique capabilities, Fusion 360 not only enhances creativity but also improves efficiency and collaboration among users.
Overview of Software
Purpose and Use Cases
Fusion 360 serves different roles, depending on the user's needs. Engineers and designers utilize it for product design, creating prototypes, and testing simulations. It finds applications in various industries including automotive, aerospace, and consumer electronics. Educators use it as a teaching tool in engineering courses, allowing students to gain hands-on experience in a real-world software environment.
Some notable use cases include:
- Rapid prototyping to validate concepts quickly.
- Generating 3D models for printing.
- Performing finite element analysis (FEA) for stress testing.
Key Features
The software possesses features that distinguish it from other CAD tools. These include:
- Cloud-Based Collaboration: Users can collaborate on projects in real-time, making it ideal for team environments.
- Integrated Simulation: The ability to run simulations within the platform allows designers to test performance and durability without external software.
- Parametric Modeling: Easily alter designs by changing parameters, enabling more efficient revisions.
With these functionalities, Fusion 360 harnesses power to transform ideas into tangible products, ensuring users have a versatile tool at their disposal.
In-Depth Review
Performance Analysis
Analyzing the performance of Fusion 360 reveals its capability to handle complex tasks without significant lag. The software can manage large assemblies efficiently, which is crucial in professional environments where precision is paramount. Users report responsive design features, meaning that as one adjusts a component, the software recalibrates immediately.
User Interface and Experience
User experience with Fusion 360 is generally positive. The interface, while sophisticated, remains accessible to those new to CAD software. The layout is designed intuitively, allowing users to locate functions swiftly. Tutorials and a supportive online community further aid in enhancing the user experience.
"Fusion 360 simplifies complex design tasks, making them more accessible for beginners while offering depth for experienced users."
In summary, Fusion 360 CAD delivers a robust set of features tailored for diverse needs in design. Its real-time collaboration, effective simulation capabilities, and user-friendly interface collectively demonstrate its potential to optimize design workflows.
Foreword to Fusion CAD
Fusion 360 is an advanced computer-aided design (CAD) tool that integrates various aspects of product design and engineering into a single platform. Its significance in today's fast-paced design environment cannot be understated. The software supports users in rapidly moving from ideation to realization, effectively bridging gaps that often exist between design, engineering, and manufacturing.
At its core, Fusion 360 offers a cloud-based approach, allowing for real-time collaboration among team members, regardless of their geographical locations. This collaborative feature fosters innovation and speeds up the design process, making it vital for teams working in a global context. With features like parametric and direct modeling, users can adjust and modify designs with ease, ensuring flexibility and efficiency.
Moreover, the integration of simulation tools helps designers evaluate their work before physical prototyping, thus minimizing resource wastage and costs. Users can also leverage manufacturing integration to streamline the path from digital design to physical product.
Choosing Fusion 360 comes with considerations. While its features are extensive, new users may face a learning curve. Additionally, the reliance on a subscription model can raise concerns for some professionals, as ongoing costs must be factored into long-term project budgets.
Here are some key points about Fusion 360's importance:
- Cloud-Based Collaboration: Foster teamwork across distances and improve communication.
- Parametric Modeling: Easier adjustments to designs facilitate innovation.
- Integration with Manufacturing: Directly link design with production processes, reducing errors.
- Accessibility: Available on multiple devices enhances user flexibility.
In this article, we will explore how Fusion 360 not only supports traditional design workflows but also adapts to the needs of contemporary engineers and designers. Given its features and usability, it serves as a comprehensive tool that can elevate the work of software developers, IT professionals, and students alike.
Overview of Computer-Aided Design
Computer-aided design (CAD) is a pivotal aspect of modern design and engineering processes. It refers to the use of software tools to create, modify, analyze, and optimize designs. CAD has transformed industries by allowing for precision and efficiency in drafting and modeling. This article explores the significance of CAD in the context of Fusion 360, highlighting its features and applications.
CAD software enhances creativity and productivity, enabling designers to visualize concepts before committing resources to physical products. This visualization reduces errors and improves quality. The capacity for rapid prototyping through CAD contributes greatly to product development cycles, ensuring that projects can progress without significant delays. The software facilitates better communication among teams through intuitive interfaces and shared files.
However, while CAD brings numerous benefits, there are also important considerations. Not every CAD tool fits all design needs. Factors such as user expertise, software capabilities, and project requirements must be taken into account. Thus, understanding the fundamentals of CAD is essential for effective design practices and to leverage tools like Fusion 360.

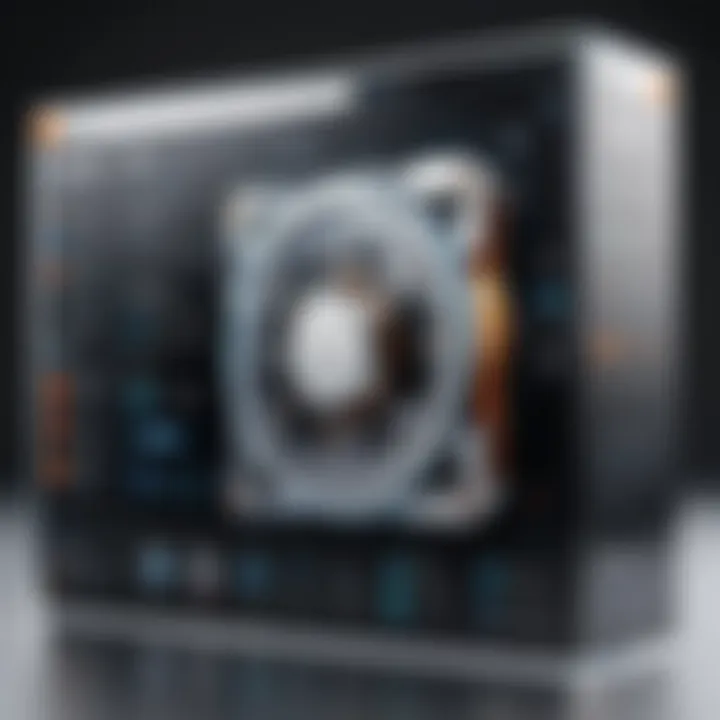
Historical Context
The journey of CAD began in the 1960s with the development of early drawing systems. These systems were largely cumbersome and limited in functionality. The first true CAD system, Sketchpad, was developed by Ivan Sutherland in 1963. Its introduction marked a turning point, demonstrating the potential of using computers for graphic design. Over the years, various advancements have paved the way for modern CAD software, evolving to meet growing demands in engineering and design.
Through the 1970s and 1980s, CAD systems became more standardized. Their adoption was spurred by the simplification of drafting processes and the rise of automated manufacturing. Early CAD programs, such as AutoCAD, allowed for 2D drafting and layout design. As technology advanced, features like 3D modeling emerged, enabling designers to create complex geometries and assemblies.
The Evolution of CAD Software
The evolution of CAD has been driven by technological advancements and the changing needs of industries. Early versions of CAD software primarily focused on 2D designs, but as computing capabilities improved, the transition to 3D was inevitable. The introduction of parametric modeling and direct modeling capabilities represented significant milestones in the evolution of CAD software. These features allow for more fluid and intuitive editing of designs, fostering a seamless user experience.
Today, cloud-based CAD systems like Fusion 360 represent the next step in this evolution. They facilitate real-time collaboration among users dispersed across various locations, an essential function in our increasingly globalized world. Moreover, features such as simulation tools, manufacturing integration, and data management empower users to handle complex projects efficiently.
CAD systems have not only improved design accuracy but also enhanced overall productivity, changing the way designers and engineers engage with their work.
As we look forward, the future of CAD software promises further innovation, particularly in areas like artificial intelligence and virtual reality, enhancing how professionals approach design tasks. This ongoing evolution underscores the importance of remaining informed about CAD advancements to leverage their full potential in various applications.
Key Features of Fusion
When evaluating Fusion 360, it is essential to understand its key features. Such features not only empower the design process but also cater to a range of user needs in various industries. This section highlights the importance of core functionalities like cloud-based collaboration, modeling techniques, simulation tools, and integration capabilities with manufacturing processes. These elements are critical for improving productivity, allowing teams to work seamlessly, and enhancing the overall design lifecycle.
Cloud-Based Collaboration
Cloud-based collaboration is a cornerstone of Fusion 360. This feature enables users to store their projects and access them from anywhere with an internet connection. With such accessibility, teams can collaborate in real-time, share projects, and receive instant feedback, which significantly streamlines the design process.
The benefits of cloud storage go beyond mere convenience. It reduces the risk of data loss and version inconsistency. Moreover, multiple users can work on the same project simultaneously, thus improving efficiency. This aspect is particularly vital for designers working in geographically dispersed teams. However, users need a reliable internet connection to leverage this feature effectively and avoid workflow interruptions.
Parametric and Direct Modeling
Fusion 360's parametric and direct modeling capabilities are fundamental to its functionality. Parametric modeling allows users to create designs by defining parameters. This means that changing one aspect of the design automatically updates related components. It improves design accuracy and flexibility, making adjustments easier as project requirements evolve.
On the other hand, direct modeling provides users with tools to manipulate geometry without the constraints imposed by parametric relationships. This is beneficial for quick iterations and modifications. The combination of both modeling techniques gives users the flexibility to choose the best approach based on their project needs. Having both methods under one roof allows for a more dynamic design process, catering to both detailed engineers and quick conceptual designers.
Simulation Tools
Simulation tools in Fusion 360 provide an avenue for validating designs before production. These tools enable designers to rigorously test their models under various conditions. By simulating stresses, strains, thermal dynamics, and fluid flow, users can anticipate potential failures or inefficient designs. This leads to more robust products and saves time and resources in the prototyping phase.
Additionally, simulation aids in making informed decisions during the design process. Calculating performance metrics early reduces revisions during later stages. It also bridges communication gaps between designers and engineers, leading to more integrated workflows. The inclusion of such tools reflects a growing demand for analytical capabilities in design software.
Manufacturing Integration
Manufacturing integration is a vital feature, allowing users to transition smoothly from design to production. Fusion 360 streamlines workflows by providing tools compatible with various machining processes. This includes CNC machining, additive manufacturing, and even injection molding. Users can prepare their designs for manufacturing right within the same platform.
This integration is crucial as it fosters a quicker transition from idea to tangible product. Additionally, it reduces errors that may arise from transferring files between multiple software applications. With everything in one place, collaborative opportunities improve, leading to a more synchronized product development lifecycle.
"Fusion 360 stands out for its ability to unify design, simulation, and manufacturing within a single platform, enhancing productivity and workflow efficiency."
User Applications of Fusion
Understanding the user applications of Fusion 360 is essential when examining its overall impact on various industries. Fusion 360 is not just a design tool; it is a versatile platform that caters to a diverse range of applications. The significance of these applications lies in their ability to enhance creativity, increase efficiency, and facilitate collaboration among users from different fields. As we delve deeper into specific user applications, it becomes clear how Fusion 360 shapes modern workflows and solutions in design.
Product Design
In the realm of product design, Fusion 360 stands out for its robust features that support the entire development process. Designers can easily craft sketches, create 3D models, and conduct simulations all in one environment. The parametric modeling capabilities allow for quick modifications, facilitating an iterative design process. Users can enhance their design capabilities through the software’s integrated simulation tools, enabling them to test product performance under various conditions.
Additionally, the collaboration features enable teams to work simultaneously, improving the speed and responsiveness of product design. Sharing designs with stakeholders becomes seamless, allowing for real-time feedback and changes. As a result, products can be brought to market faster without compromising quality.
Architecture and Engineering
Fusion 360 serves as an effective tool in architecture and engineering, bridging the gap between design and real-world application. Architectural professionals can utilize the software's parametric tools for building design, creating structural models with accuracy. The ability to visualize complex structures in a 3D environment assists in better decision-making. Such visualization helps to determine design feasibility, which is critical in large-scale projects.
In engineering, the software’s simulation features enable engineers to test materials and stress points before actual production. These capabilities reduce potential errors and risks during later stages of project execution. The integration of design and structural analysis ensures the end product is both functional and safe, which is vital in engineering disciplines.
Animation and Visual Effects
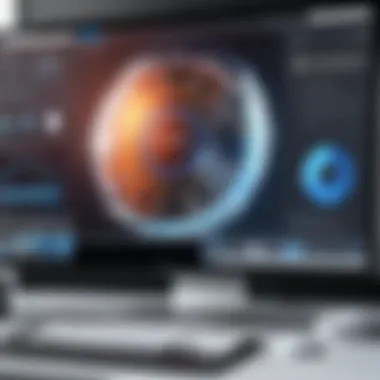
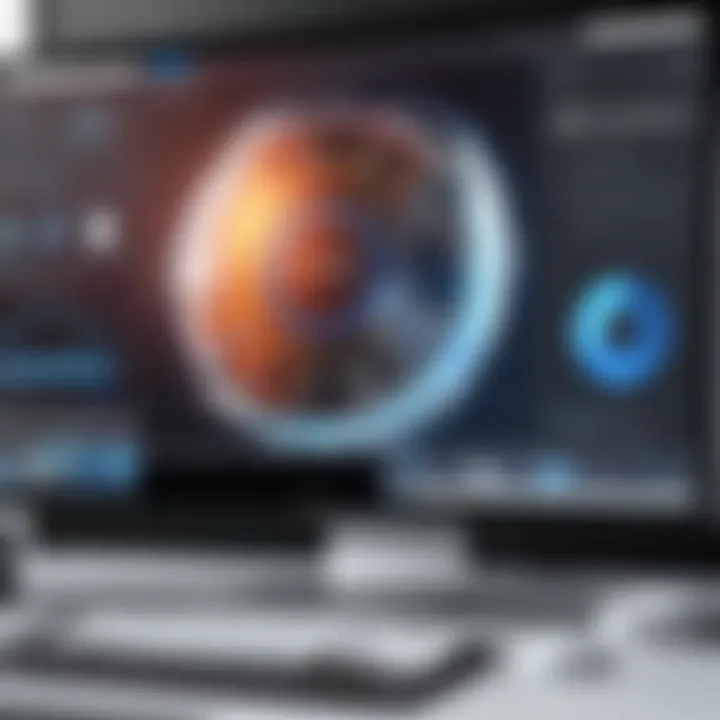
For creative professionals in animation and visual effects, Fusion 360 offers unique capabilities that can enhance storytelling in various media. Users benefit from the software’s ability to create intricate models which can be animated efficiently, providing a smooth transition from design to motion. This application can be especially critical for industries such as video game design and film production, where detailed models and realistic animations are required.
The software also supports rendering techniques, giving users the tools to produce visually appealing graphics. This ability allows designers to present their ideas convincingly, ensuring that stakeholders can appreciate the intended outcome. Consequently, Fusion 360 has become an integral part of the animation pipeline for many professionals.
Educational Uses
In educational settings, Fusion 360 has made a considerable impact on how design and engineering are taught. Its intuitive interface allows students to engage with CAD tools from an early stage, making it an excellent choice for learning environments. Institutions can easily integrate Fusion 360 into their curricula across various disciplines such as design, engineering, and architecture.
Furthermore, the ability to collaborate on projects reflects real-world scenarios students will face in their professional careers. Educators can utilize the software to promote hands-on experience, providing students with practical skills that are highly sought after in the job market. By engaging in project-based learning with Fusion 360, students develop critical problem-solving skills and a deep understanding of design principles.
Comparative Analysis with Other CAD Software
In the realm of computer-aided design, selecting the right software plays a crucial role in the effectiveness and efficiency of design workflows. A comparative analysis of Fusion 360 with other prominent CAD software provides insights into its unique features and benefits. By examining different CAD tools, users can make informed decisions based on their specific requirements and preferences. This section evaluates Fusion 360 in relation to SolidWorks, AutoCAD, and Rhino, shedding light on their strengths and weaknesses against each other.
Fusion vs. SolidWorks
Fusion 360 and SolidWorks are both powerful tools, but they serve different user needs. SolidWorks, traditionally favored by engineers for its robust parametric design capabilities, has a long-standing reputation in the industry. One of its key features is its highly detailed mechanical design capability, which is ideal for large assemblies and complex parts.
On the other hand, Fusion 360 offers a more integrated platform combining CAD, CAM, and CAE functionalities. This is beneficial for users who engage in end-to-end product development. Another standout feature of Fusion 360 is its cloud-based collaboration. It allows real-time teamwork among users, which SolidWorks does not inherently provide. In terms of pricing, Fusion 360 typically offers more flexible subscription models, making it accessible for startups and individual users.
Fusion vs. AutoCAD
AutoCAD is synonymous with 2D drafting and has been a cornerstone in the design industry for decades. Fusion 360, however, includes both 2D and 3D modeling capabilities alongside advanced simulation tools. While AutoCAD is powerful for creating detailed blueprints and layouts, Fusion 360 takes the lead with its ability to handle complex 3D models.
Fusion 360’s data management options are also superior, allowing users to keep track of design changes easily and collaborate with teams remotely. Furthermore, Fusion 360's cloud integration allows for seamless access to designs from different devices without the need for specific software installations, a significant advantage for dynamic work environments.
Fusion vs. Rhino
Rhino is known for its flexibility and capability in handling freeform surface modeling, often appealing to designers in architecture and industrial design. In contrast, Fusion 360 is better optimized for product design and manufacturing workflows. Rhino excels in creating complex geometries, while Fusion 360 integrates simulation and manufacturing tools that offer a more comprehensive approach to product development.
As for performance, Fusion 360 tends to be more resource-efficient, especially on modest hardware. This is crucial for teams who need to operate on varying hardware setups. Additionally, the user-friendly interface in Fusion 360 allows users to get started faster compared to Rhino, which can have a steeper learning curve due to its wide array of features.
It's essential to assess the specific needs of your projects to determine which CAD platform aligns best with your goals.
In summary, the comparative analysis highlights that each software has its own strengths. Fusion 360 is advantageous for collaborative, integrated product design, while SolidWorks, AutoCAD, and Rhino excel in their specialized features. Understanding these distinctions can greatly enhance productivity and effectiveness in design projects.
Strategies for Effective Implementation
The strategies for effective implementation of Fusion 360 CAD are essential in maximizing the utility of this software in diverse projects. Successful implementation can streamline design workflows, facilitating better collaboration and project management. It focuses on specific elements such as project setup, collaboration techniques, and data management practices. Each of these aspects contributes to an efficient work environment that leverages the full potential of Fusion 360.
Setting Up a Project
Setting up a project in Fusion 360 requires clear planning and understanding of the project objectives. Start by defining the goals and specifications. This can include aspects such as the design requirements, deadlines, and resource allocation. In Fusion 360, creating a new project is straightforward. Users should navigate to the Data Panel and choose to create a new project.
Once the project is created, organize files systematically. Use folders for various elements like sketches, models, and assemblies. Additionally, naming conventions are important. A clear naming system will enhance searchability and help team members locate files quickly. Regular backups are also crucial, as losing data can disrupt the workflow. Emphasizing security measures for project files can protect valuable assets.
Team Collaboration Techniques
Collaboration is a fundamental component of successful project execution in Fusion 360. Given its cloud-based capabilities, it allows multiple users to work on the same project simultaneously. To enhance teamwork, establish clear communication protocols. Use tools like comments and tagging within the app. This fosters an environment where feedback can be easily exchanged.
Introducing version control practices can also help track changes made by team members, ensuring that everyone is on the same page. Regular team meetings can further align efforts and discuss progress. These techniques not only improve teamwork but create a culture that values shared input and collective problem-solving.
Data Management Practices
Data management in Fusion 360 is critical for maintaining project integrity and efficiency. Effective data management strategies involve organizing files systematically and maintaining proper documentation. Setting rules for file naming and versioning will avoid confusion and duplication.
Utilize the Data Panel to its full potential. It provides a clear view of project files and preserves the history of changes made. Regular audits of project data can identify unused files, simplifying your workspace and improving loading times.
Moreover, establish procedures for data sharing. Clear paths for how files will be shared, edited, or archived can save time and reduce frustration among the team members. A well-organized data structure facilitates smoother collaborations and helps in maintaining productivity.
"Effective implementation strategies in Fusion 360 not only improve workflows but ultimately enhance the quality of the projects being developed."
By focusing on these strategies, users can ensure that their experience with Fusion 360 is not only productive but also enjoyable. Empowering teams through effective project setup, collaboration methods, and robust data management will lead to successful design outcomes.
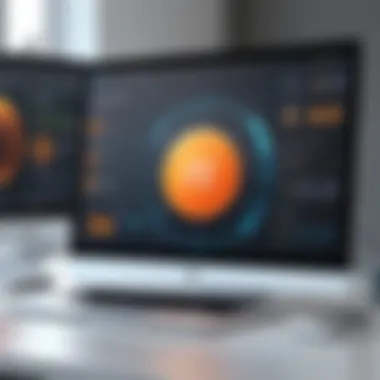
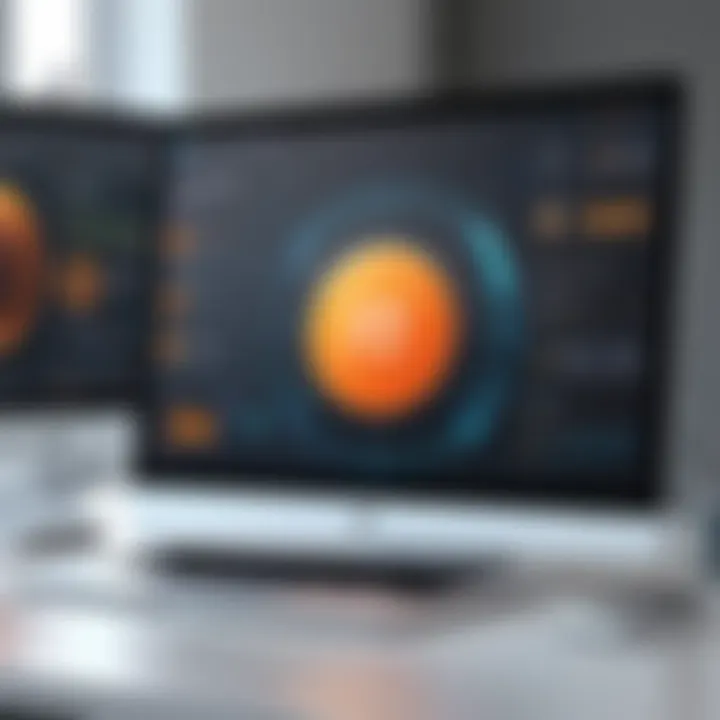
Challenges and Limitations of Fusion
Understanding the challenges and limitations of Fusion 360 is crucial for both new and experienced users. Recognizing these elements helps in setting practical expectations and informs users about the potential obstacles they might face. Each software has its strengths, but also weaknesses. While Fusion 360 is a powerful tool, it does present certain hurdles that can impact productivity and user satisfaction.
Learning Curve for New Users
One significant challenge is the learning curve that new users must navigate. Fusion 360 integrates a variety of tools for modeling, simulation, and collaboration, which can be overwhelming for beginners. The interface, while intuitive to some, requires familiarity with CAD concepts and workflows. Users often report that basic tasks take longer as they try to familiarize themselves with the numerous features available.
Additionally, users who have experience with other CAD software might find the transition particularly jarring. The differing design philosophies mean that established users often need time to adapt. To mitigate this, Autodesk provides resources and tutorials, but self-directed learning can still be daunting. New users should expect to invest time in training to effectively harness the program's capabilities.
Performance Issues on Low-End Hardware
Another challenge is performance inconsistencies on lower-end hardware. Fusion 360 is a robust application that relies heavily on computational power. As a result, users running the software on outdated systems may experience lag, crashes, or slow rendering times. This can lead to frustration, especially during critical project deadlines.
To achieve optimal performance, it is recommended to have a computer that meets the official system requirements. Users should consider upgrading their hardware if they plan to engage in complex modeling tasks. The software's demands can hinder productivity for those without access to high-performance devices, making it a vital consideration for teams with varying equipment.
Subscription Model Concerns
Lastly, the subscription model of Fusion 360 raises concerns for some users. While the model allows for regular updates and access to the latest features, it can lead to long-term costs that may be problematic for small businesses or individual users. This subscription-based pricing means users must continuously factor in the monthly or annual fees when budgeting for design tools.
Moreover, users are often hesitant to invest heavily in a subscription service, feeling uncertain about their return on investment. It can create pressure, especially if projects are unpredictable. Some may prefer a one-time purchase model, believing it offers more control over their expenses.
"Fusion 360 provides great features, but the subscription and performance issues can trouble many users."
Future Trends in CAD Software
The realm of computer-aided design (CAD) is consistently evolving. As we look ahead, certain trends emerge that will significantly shape the landscape of CAD software like Fusion 360. Understanding these trends is crucial for professionals, educators, and developers alike. The importance of these trends cannot be overstated, as they reflect the needs of the industry and the direction technology is heading. Below, we explore three significant future trends in CAD software: AI integration, sustainability, and advancements in AR/VR applications.
AI Integration in Design
Artificial Intelligence is increasingly being integrated into design processes. This shift promises to enhance productivity and creativity. AI can automate repetitive tasks and analyze complex datasets, aiding designers in making better-informed decisions. With tools like Autodesk's own generative design, users can input parameters such as materials and budget, and let the AI propose optimal design solutions. This saves time and fosters innovation. AI’s predictive capabilities help in anticipating issues that may arise during the manufacturing process, leading to a more streamlined workflow.
Increased Focus on Sustainability
Sustainability is becoming a priority in product and industrial design. Designers are recognizing their responsibility to reduce the environmental impact of their work. Future CAD software will likely incorporate features that help users analyze the sustainability of their designs. This includes assessing materials for their environmental footprint and energy efficiency. By evaluating the lifecycle of products, designers can create solutions that are not only efficient but also environmentally friendly. The incorporation of sustainability practices in CAD workflows can lead to more ethical design choices and compliance with regulations.
Advancements in AR/VR Applications
The world of augmented reality (AR) and virtual reality (VR) presents new opportunities for design and visualization. These technologies enable users to interact with their designs in a more immersive environment. For instance, architects can walk through their designs before construction begins, providing a clearer understanding of spatial relationships. Future CAD software is expected to offer improved AR/VR capabilities, enhancing collaboration among teams. Whether it’s for client presentations or internal reviews, visualizing projects in 3D space bridges gaps in communication.
"The future of CAD software lies in its adaptability to new technologies, ensuring designers can create in ways previously thought impossible."
In summary, the future trends in CAD software and specifically Fusion 360 offer exciting possibilities. AI integration, sustainability considerations, and advancements in AR/VR applications stand out as significant elements. These trends not only provide practical benefits such as improved efficiency and collaboration but also promote responsible design practices. As these technologies become more mainstream, CAD software will need to adapt to stay relevant and beneficial to its users.
The End
Benefits of Fusion include:
- Enhanced collaboration, made possible through its cloud-based architecture. It allows teams to work together seamlessly in real-time, no matter where they are located.
- Versatile modeling options, with both parametric and direct modeling capabilities. This flexibility caters to various design needs and enhances user creativity.
- Integrated simulation tools that help predict product performance early in the design process, reducing the chances of costly revisions later on.
- Comprehensive manufacturing integration ensures that designs can transition smoothly from conceptualization to production.
However, the article also touches on essential considerations. Users must be aware of the learning curve associated with the software, especially for newcomers. Performance issues may arise on lower-end hardware, which is a critical aspect to consider when planning for deployment in educational or professional environments. Additionally, the subscription model may raise questions about long-term costs, which can impact budgeting decisions for both individuals and organizations.
Importantly, the future of CAD software is continuously evolving. Trends indicate that AI integration, increased sustainability efforts, and advancements in AR/VR applications are shaping how designers interact with software like Fusion 360. All these elements combine to make Fusion 360 a notable leader in the field, essential for anyone serious about modern design.
In summary, embracing the full capabilities of Fusion 360 CAD can significantly enhance design workflows. A thorough understanding of its features and considerations will equip users with the knowledge needed to utilize this powerful tool effectively.
Importance of References
References substantiate the content. They provide authority to the discussion on Fusion 360's capabilities, applications, and relevant comparisons with competing software. Properly cited resources facilitate a deeper understanding of the software by allowing readers to explore original sources. This is particularly beneficial for professionals and students in IT-related fields who might need to validate findings or seek further detail.
Benefits of Comprehensive References
- Credibility: Referencing external, authoritative publications enhances the overall credibility of the article.
- Clarity: Readers can refer to original research, historical accounts, or specific case studies that clarify complex subjects, which can sometimes be lacking in brief descriptions.
- Engagement: Referencing engaging platforms, such as Reddit or Facebook groups related to CAD, allows readers to explore community discussions and insights beyond traditional literature.
Considerations for Including References
It is essential to ensure that references are current and relevant. In the fast-evolving field of CAD, outdated information may mislead readers. Moreover, including varied types of references, such as academic articles, user manuals, and community forums, can enrich the narrative, making it more well-rounded and engaging.
"References are not just citations; they are gateways to further exploration and understanding."